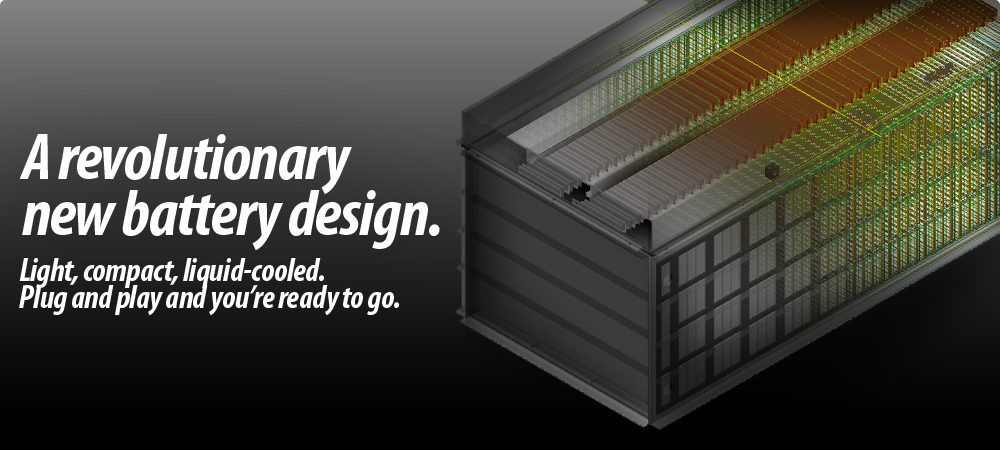
Drawbacks of existing battery packs
Existing battery packs are plagued by the three problems of short service life, short range and the inability for it to charge/ discharge in temperature extremes. It is nearly impossible to charge below 0°C. During other seasons, when the working temperatures in battery packs can reach more than 60°C after heavy charging and discharging, it will be very hard to discharge once past 60°C. All of these impede the widespread adoption of electric vehicles as a primary means of transportation.
Current-technology battery packs have very inefficient cooling systems, directly contributing to the problem of short service life.
Battery modules, each with several battery cells, are connected side-by-side in an array. Attached to the array is a heat sink, with a coolant loop running through it. The result is that only a portion of each module receives the cooling effect due to thermal insulation. Heat sinks, besides being thick and heavy, also have limited cooling effectiveness.
What happens is that the temperature will differ from module to module, cell to cell. Within the same cell, different regions may also have different temperatures.
Even if we were to design a battery pack with heat sinks for every single cell, the result would be a battery pack with impractical weight and volume.
As cells and modules in a battery pack are interlinked, failure of one cell can drastically affect the lifespan of the entire battery pack. Once the cells are produced and assembled into battery packs, the only factor that is able to affect its consistency and uniformity is the temperature of each cell. Temperature changes can affect the cells’ internal resistance, and changes to internal resistance can in turn affect the rate of temperature change. The existence of a temperature gradient between cells will cause different rates of cell ageing, resulting in certain cells having shorter lifespan.
Battery cells have an optimal working temperature range of 15-35°C. Every increase of 10°C will halve its service life.
The service life of a single cell can reach upwards of 1000 cycles, but once connected in a battery pack, their collective service life is only a few hundred.
Our solution
Identifying the root of the problem – inefficient cooling – is the easy part. The hard part is coming up with a practical solution to all of this.
Energeia Labs has developed a novel battery pack design which is not only more compact and lightweight, but also solves the longstanding issue of inefficient cooling, improving battery longevity and lowering costs. This design is designated BP-1.

Consistency and uniformity of the battery cells are critical for durability and effectiveness of the whole battery pack. BP-1 manages to have liquid cooling/ heating white maintaining a compact and lightweight design. The battery cells in BP-1 are able to be kept cool without the formation of a temperature gradient, allowing for longer cell lifespan.
How this is done is from our novel design that allows liquid coolant to be delivered to all areas of the battery cells, ensuring even and effective cooling. Neither safety nor cooling efficiency is compromised in the process.
The parts required to construct the battery pack are easy to fabricate, and the assembly process is straightforward and low-cost. The result is a liquid-cooled, lightweight and compact battery pack, possessing large energy capacity, high power and longevity.
Because of the nature of its design, it can be customized according to the dimensions of different battery cells.
When cells are fixed into place with thermal silicone, this can both reduce friction and vibrations, and also increase thermal conductivity, between the cells and the cooling ducts.
BP-1 is also plug-and-play capable. How we tackle the issues of range anxiety and the inability for charge/ discharge in temperature extremes is further illustrated in the ‘Applications’ page.
To see how BP-1 matches up to existing technology, visit our ‘Advantages’ page.
Our ‘Specifications’ page has data pertaining to BP-1.